3.4.2 - Processos contínuos
Existem diversos processos para a fabricação contínua de blocos dos diferentes tipos de espumas flexíveis, cada qual tendo suas vantagens e diferenças quanto à conversão e eficiência. Por exemplo, as espumas de poliéter de grau mobília são produzidas mais eficazmente em máquinas Maxfoam ou Vertifoam. As espumas de poliéter de grau técnico são melhor produzidas por derramamento em máquinas Maxfoam ou Convencionais. As espumas de poliéster de grau standard são fabricadas mais eficazmente nas máquinas Convencionais. As espuma de poliéster de grau técnico e automobilístico são melhor fabricadas por derramamento em máquinas Convencionais. Finalmente, uma combinação das tecnologias Maxfoam e Convencional, na máquina do tipo Ultima permite a produção de toda a gama de espumas de poliéter e de poliéster.
A produção contínua de blocos de espuma flexível (Figura 3.9) consiste nas seguintes etapas: 1) Armazenagem e condicionamento térmico das matérias-primas; 2) Medição e mistura; 3) Formação do bloco; 4) Cura; e 5) Acabamento.
1)
Matérias-primas; 2) Tanques diários; 3) Cabeça misturadora; 4) Bloco da espuma;
5) Corte vertical; 6) Cura final.
Figura
3.9 – Esquema do processo contínuo
Os polióis e diisocianatos são normalmente em tambores ou contêineres e estocados em tanques de 10 a 30 m3 de capacidade. Como as reações são influenciadas pela temperatura é importante o condicionamento das matérias-primas entre 20-25oC, podendo nas regiões quentes ser superior a 30oC. O TDI congela a 17oC, produzindo cristais brancos e semitransparentes do isômero 2,4, e a sua contaminação com água produz uréia branca e opaca. Os demais aditivos são normalmente armazenados em tambores. A dosagem precisa das matérias-primas, com bombas dosadoras, é importante e as vazões devem ser constantes. Em máquinas de baixa pressão as linhas operam entre 1-15 kgf/cm2, e a câmara de mistura, dotada de agitador mecânico de alto cisalhamento, opera entre 0-1 kgf/cm2, em rotações entre 2.000 e 6.000 rpm. Nas máquinas de alta pressão as linhas operam entre 20-100 kgf/cm2, e as matérias primas são misturadas por choque e agitação mecânica menos eficiente, entre 0,5 a 3 kgf/cm2.
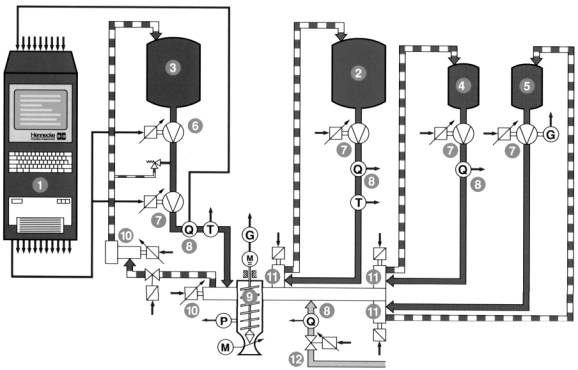
1)
Central de controle; 2) Tanque do poliol; 3) Tanque do isocianato; 4) Vaso dos
aditivos; 5) Vaso da pasta de pigmento; 6) Bomba de alimentação; 7) Bombas dosadoras;
8) Medidores de fluxo; 9) Agitador; 10) Válvula de controleda injeção do isocianato;
11) Válvula de produção / recirculação; 12) Admissão de ar.Máquinas de grande capacidade podem ter fluxos suficientemente grandes para ser independente para cada componente. Em outras o poliol polimérico, retardantes de chama e corantes podem ser misturados ao poliol. O agente de expansão pode ser dosado em fluxo separado e alimentado na câmara de mistura ou, um pouco antes na linha do poliol, ou ainda ser misturado ao poliol. O ar de nucleação também deve ser introduzido na linha do poliol. Água, amina e silicone não hidrolisável podem constituir uma corrente, porém o octoato estanoso deve ser adicionado separadamente, em solução de 10 a 50% em poliol seco, para possibilitar uma medida eficiente do fluxo. No início da produção deve-se: 1) ligar o agitador, 2) o fluxo do poliol, 3) o fluxo do agente de expansão e demais aditivos, 4) o fluxo de isocianato, e no fim deve-se proceder na ordem inversa.